比亚迪海豹正式上市了。我知道这车很爆,我们的视频、帖子、文章也很全面,我就来梳理一下这个 CTB 技术吧。
集成之路
电动车围绕电池的话题从来不断,同样作为汽车供应商,电池厂家的身家和地位,大家可以参考宁德时代。
CTB(Cell to Body)、CTC(Cell to Chassis)、CTP(Cell to Pack)三个概念,随之火了>起来。
最初,动力电池行业标准各异,CTM(Cell to Module)开始成为主流,一般遵循是「电芯-模组-电池包」最后到车身底盘,这样的三级装配流程。
而 CTP 技术,就是拿掉了这三级中的模组,可以进一步给电池包塞进去更多的电池。
CTB 和 CTC 从大类上来说,思路一致,都是通过进一步剪除电池包壳体,进一步释放空间给电池。
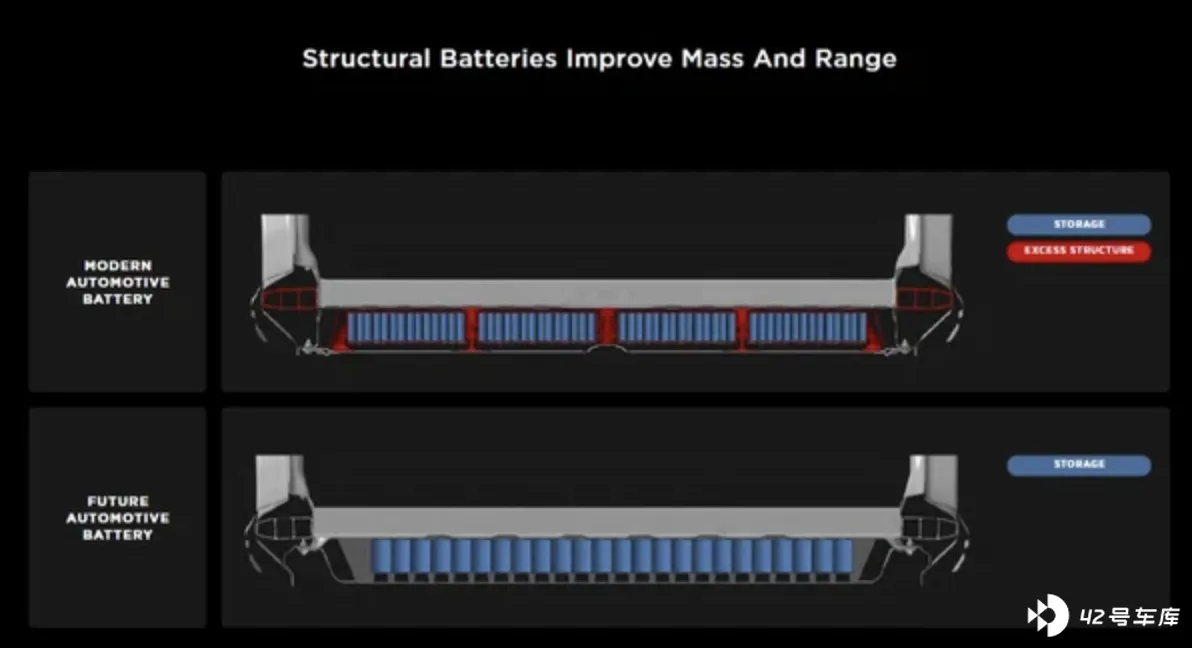
CTC 名声大噪和特斯拉分不开。
2020 年的特斯拉电池日上,>特斯拉展示了 CTC(Cell to Chassis)封装的 4680 电池。电池通过类蜂窝状的站立排列,电池包成为了和底盘融为一体的结构件,承接受力。
由于电池包支撑结构件的消失,实现了更紧凑的电池排布,所以电池可以位于汽车更加中央的位置,重量分布更>接近重心,角惯量更小,对极限的操控响应有提升。另外还顺带增强了侧面碰撞中对电池的保护。
马一龙怕我们不懂,还在 Battery Day 上绘声绘色的用「花样滑冰」举例子:在进行旋转动作时,手臂的屈伸会直接影响角惯量,从而影响转速。手臂收紧,>角惯量小,由于角动量守恒定律,角速度增加。用人话说就是,重量分布越集中于重心,车子的操控越灵活。
在特斯拉的 CTC 封装过程中,「多功能结构胶」的使用至关重要,特斯拉希望具有结构粘合以及耐火阻燃的双重特性。
我个人倾向于认为 CTC 对电池和车身的集成更深入,而且搭配一体压铸效果更佳,整车扭转刚度提升应该比较明显。
比亚迪的 CTB
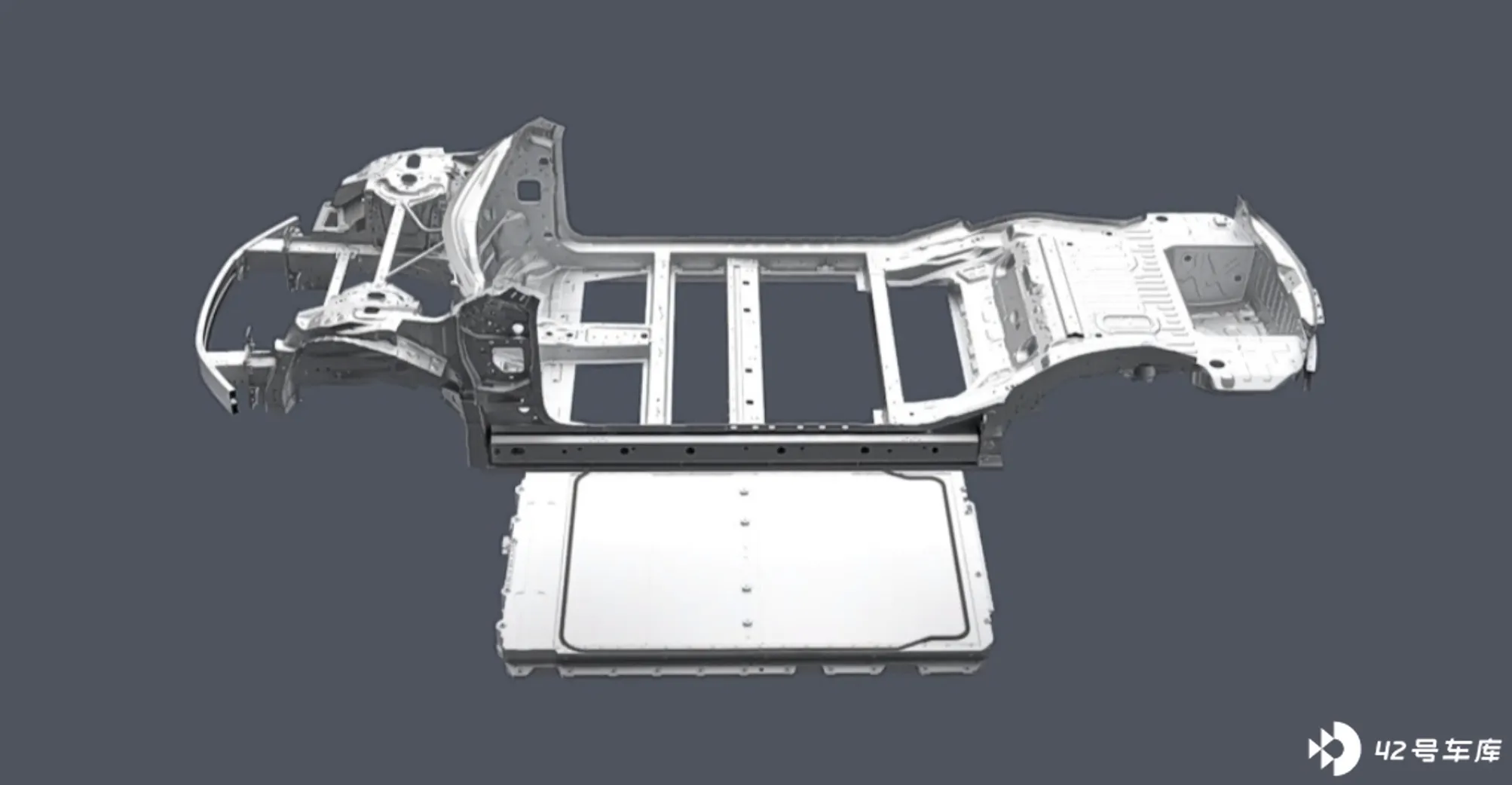
比亚迪的 CTB,就是把车身底板面板与电池包上盖板进行了集成,用比亚迪自己的话来说,就是「整车三明治」。
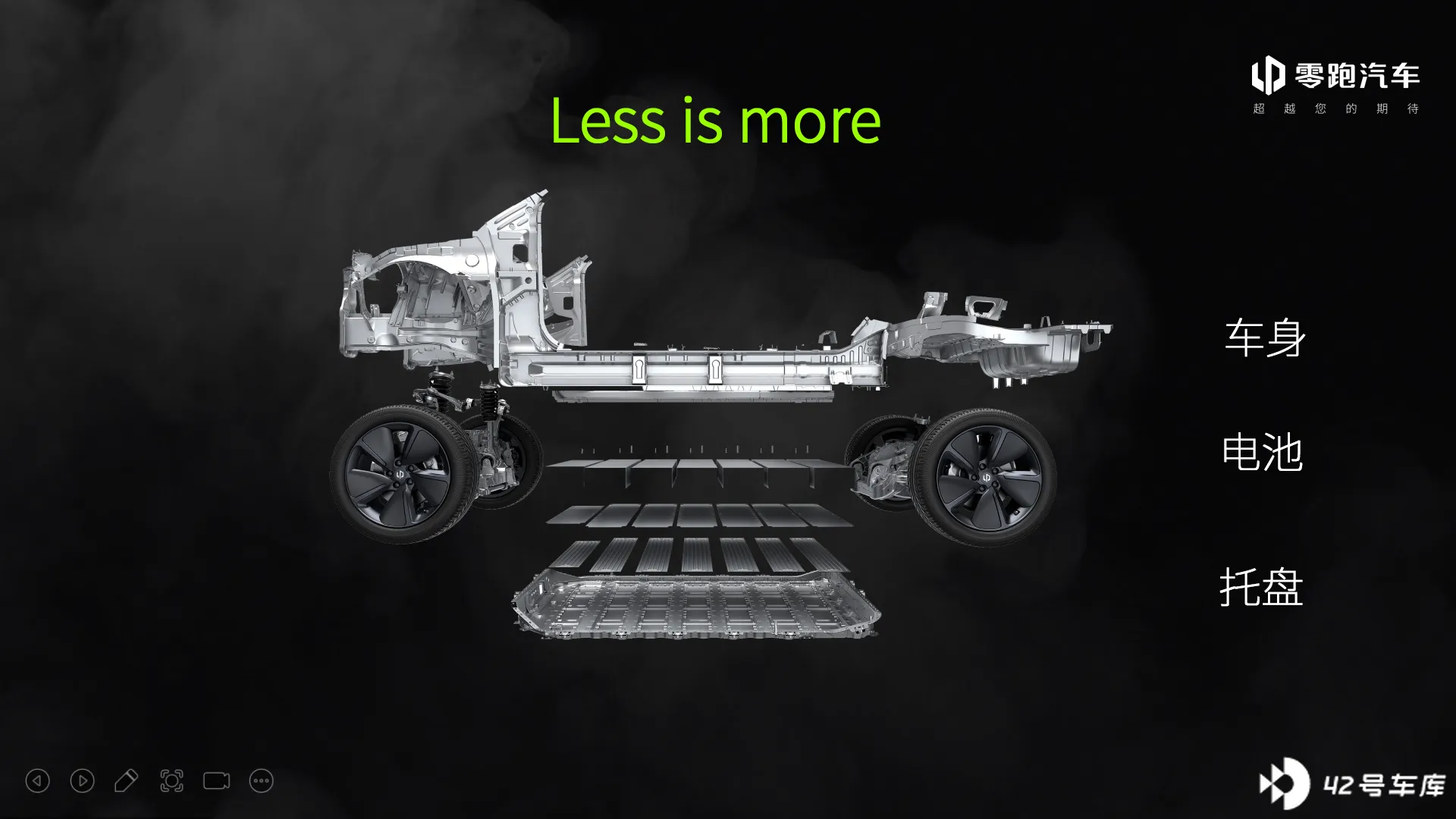
前几天的零跑 C01 的 CTC >与比亚迪的 CTB 有些类似,都要是去掉了电池包的物理存在。而零跑的思路,则是用车身的底板直接当作电池包的上盖板,电芯与模组,从下集成到车体中。
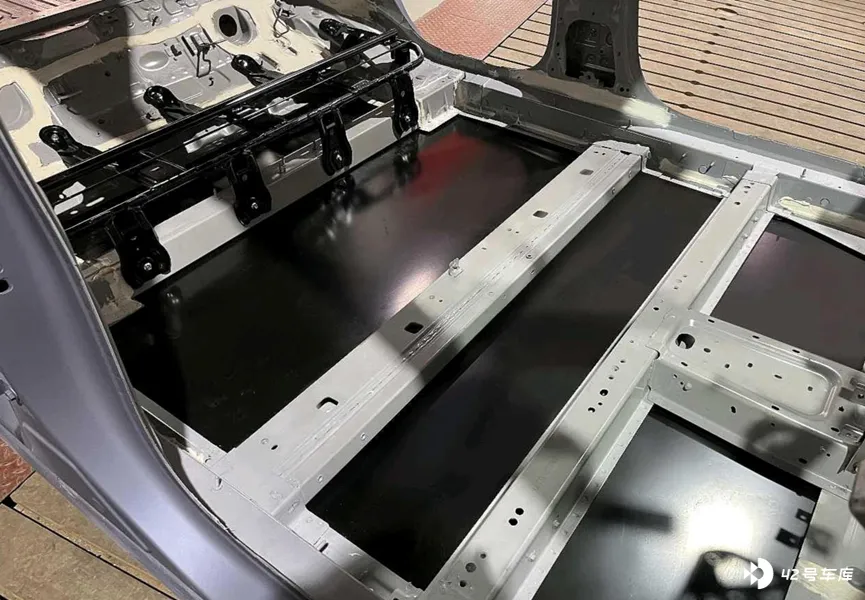
其实从曝光的图片上看,车身底部依然保留了横梁来加强整车扭转刚度,并不是完全让电池受力。而且座椅会通过横梁进行固定,>而不是像特斯拉「直接坐在电池上」。
但是显而易见,这种设计将会使乘员的脚,直接通过地毯与电池上盖板进行接触,免不>了会承受力量冲击。我比较好奇,比亚迪会通过什么材料来消解这个问题。
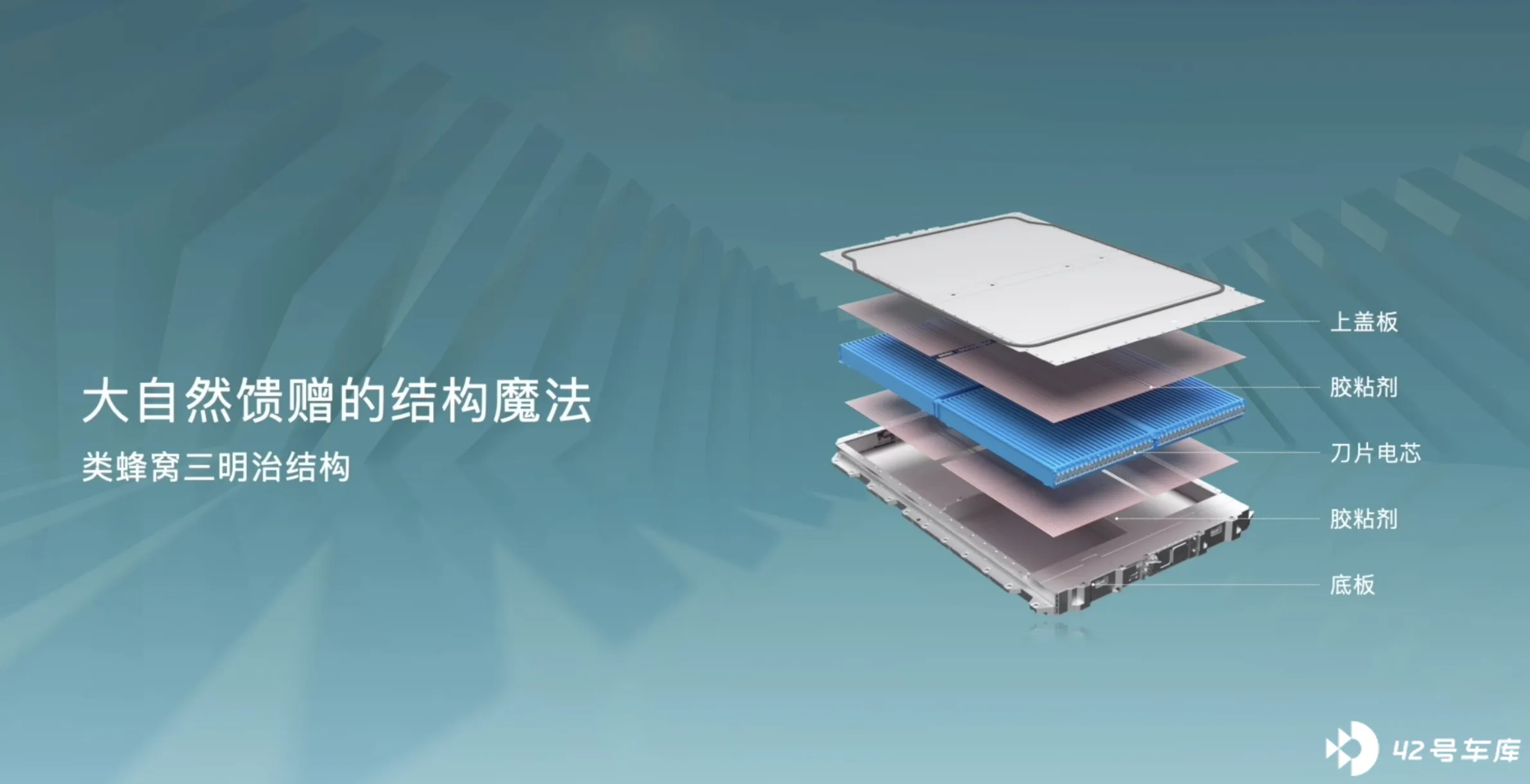
这张图,其实还能看到竖置的刀片电池,电芯依然分为四个超大模组,模组之间,依然有物理区隔,防止热失控蔓延。
效果:
-
电池能量密度的提升>:在 2,920 mm 的轴距下,塞进了一块 82 kWh 的磷酸铁锂电池(小鹏 P7 轴距 2998 mm,最大 81 kWh 电池);
-
电池垂直>高度的释放:增加了 10 mm 的垂直空间,整车高度降低了 15 mm;
-
对于操控来说:低质心(467 mm)、黄金轴荷比、角惯量小、扭转刚度(40,500 N·m)的优势,也能体现出来;
-
缺点:维修成本和难度大幅提升。料想一下,电池挤压磕碰,我们现>在都需要花十几万换电池,而在 CTB、CTC 之后,这个成本还会上升,甚至直接换车。(狗头)
写在最后
扯了这么多>,其实都是理论上的。但总体来说,电池的集成化,是大趋势。比亚迪和零跑开始尝鲜了,其他车企要怎么选呢?