作者: 苏秦
自锂离子电池进入市场以来,凭借寿命长、容量大、无记忆效应等优势被广泛应用,随着使用锂电池的频率增加,在低温情况下使用容量低、衰减严重、循环倍率性能差、脱嵌锂不平衡的现象层出不穷。
新能源动力电池组中的散热系统不仅是制约充电速率的一大原因,还是影响新能源动力电池组降温速度的 「罪魁祸首」。因此,电池热管理是电动汽车关键技术之一,电池热控管理技术影响着动力电池的安全性、续航里程、寿命与快充能力等,从而控制电池包(PACK)内的温度环境对电芯的可靠性、寿命以及吸能的影响。
动力电池热管理经历的几个阶段
目前动力电池系统的热管理系统通过冷却与加热来实现的主要可分为四类,分别是自然冷却、风冷、液冷与直冷四种冷却方式。其中自然冷却是被动式的热管理方式;风冷、液冷、直冷属于主动式(散热),它们之间也存在差异性,主要区别是换热介质的不同。

风冷
在风冷模式中,冷风以低温空气为介质,通过热对流(自然风、风机,配合汽车自带的蒸发器)来降低电池温度,以此达到散热的目的。该系统结构简单,便于维护,早期被广泛运用于电动乘用车市场,比如日产聆风、起亚 Soul EV 等,此前一直被广泛使用在电动公共汽车、电动物流车中。
只是风冷技术与液冷技术相比,风冷等技术与电池表面之间的热交换系数比较低,加上电池箱的密封设计较难,防尘、防水效果较差,因此冷却、加热速度慢,电池箱内的温度分布不均匀也就不受控制,也就被摒弃使用了。
水冷
水冷散热系统主要有电子水泵、换热器、电池散热片、PTC 加热器以及膨胀水箱,水冷技术是一种基于液体交换的冷却技术,一般会将散热器与制冷循环联合使用,通过制冷剂将电池的热量带走,这种模式比风冷技术更高,使电动车电池组内部的温度分布更均匀,与车辆的冷却系统整合在一起,达到电池壁之间的交换系统高、冷却、加热速度快的优势。

但水冷技术系统的缺点比较明显,系统复杂,重量大,维修与保养难度大还存在漏液的可能。
目前采用水冷技术的汽车包括特斯拉等品牌车型,其中特斯拉 Model S 车型为了起到降温的作用以及降低电池自燃的风险,将电池排布、热管理系统以及电池管理系统做了进一步的优化,其密封在一个钢制隔间中,液冷系统具体到每一个电池单元进行冷却,以达到降低彼此的温度。
液冷
液冷冷却技术主要通过冷却液为电池系统达到降温的效果,通过冷凝器、压缩机等设备为冷却液强制降温,低温冷却液在电池系统内部与电芯发生热交换以后,再流回热交换器与低温制冷剂进行热交换,从而将电池产生的热量带回电池系统。因此液冷系统的优势就比较灵活,可以将单个电池或模块沉浸在液体中,或在电池模块间设置冷却通道、电池底部设置冷却板,需要注意的是电池与液体直接接触时,液体保持绝缘,否则就会造成短路的问题。不过液冷技术对液冷系统的气密性要求很高,需要考虑机械强度、耐震动性以及寿命要求。

只不过主流电动车电池热管理系统采用的液冷技术仍然存在部分正在攻克的难题,比如:
(a)热均衡性差:从原理上讲液冷方法属于温差换热原理,无法避免电池模组内部温差问题,温差导致模组不同单电池充放电过程中的过充、过放与充放电不足,造成电池不安全、电池寿命短的问题出现。
(b)换热功率受限:由于可控温差与环境密不可分,冷板的液冷换热功率与温差、流量都有关,当电池充放电速度受散热速率限制时,就会造成热失控风险。
(c)热失控风险高:电池单元短时间基于温差显热散热速率有限,发热与温升之间产生的正循环会发生燃烧、爆炸的现象,极易出现热失控的情况。
(d)寄生功耗大:液冷循环阻力较大,冷板流通量较小,当换热量较大时,流速就很大,循环压损大,功耗就大,从而降低了电池的续航里程。
目前液冷是众多电动乘用车的优选方案,采取液冷的冷却方案也是众多行业的 「兵家必争之地」。
8 月 12 日,绿源举行了 「液冷超续航 2.0 品质中国行」 发布会,表示全新一代长续航电动车液冷超续航 2.0 系列正式上市,有效提高电动车的寿命,轻松实现一部车骑 10 年不衰竭;蔚来计划在今年陆续推出液冷超级快充桩;互联网巨头阿里巴巴甚至说要计划 3-5 年的时间用液冷代替风冷,将液冷变成服务器默认配置;华为也计划将围绕数据中心直冷难题持续攻关,使用液冷方案、冷却系统进行散热。
从电池发展上看,风冷、水冷技术已经变成了过去式,液冷技术处于现在进行时,而直冷技术是将来式。


为何说直冷是未来发展的主流?
先来说下原理:冷媒直冷技术的原理与空调很相似,都是通过压缩机将制冷剂气体压缩成高温高压的气体,然后进入前端冷凝器后,将制冷剂气体被冷凝成高温中压的液体,高温中压的液体通过膨胀阀碰撞,将低温低压的两相流进入蒸发器,蒸发器通过车舱空调蒸发器或是电池包内的冷板,制冷剂吸收热然后不断蒸发,最后变成气体通过膨胀阀回到压缩机完成整个循环。
当前将直冷系统做的有显著效果的车企之一有比亚迪,比亚迪海豚车型集中了比亚迪一直探索应用的两个技术,一个是热泵,一个是直冷,通过这两个技术组成 「热管理集成模板」,将电机电控处产生的余热再被利用起来,用于低温时对电池的加热。热泵有助于进一步提高整车电能的利用率,节省电量;直冷进一步提高对电池的冷却效果,在同等条件下,直冷技术的效果远远比液冷技术更高,尤其是均温性上。

直冷的优势:
性能与 COP
直冷系统可以减少一次换热过程,减少一次换热热阻,降低换热温差,传热性能好,且制冷剂在电池冷板内沸腾化热,换热能力显著增强。
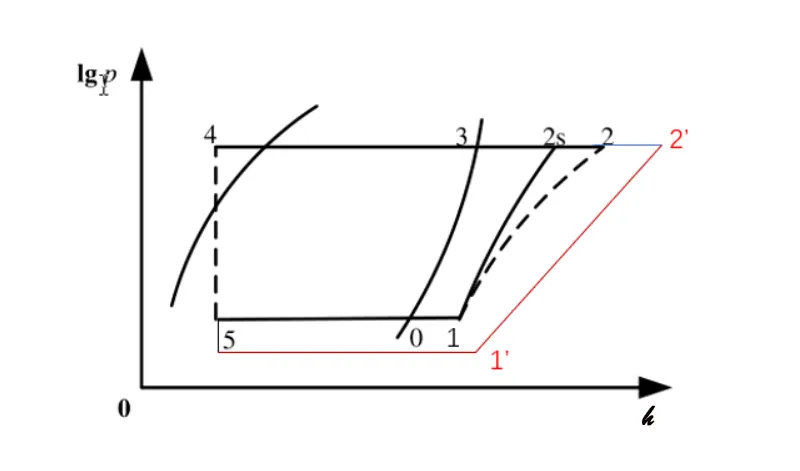
系统复杂度
原有的系统要借助 Chiller 来完成,然后再通过水泵水管到水冷板上,直冷技术可以直接将电池回路的水系统彻底消除,将 Chiller 原有的制冷剂部分做成一个大板放在电池里,减少了 Chiller、水路以及水泵等部件的占用空间。
另外,从对标指标中可以看出,直冷系统的效率比液冷高出 3-4 倍;甚至满足快充需求、结构紧凑、避免乙二醇溶液在电池箱体内部流动。
看完直冷技术的优势后,或许很多人会好奇,为何大家不用直冷技术而是依然在大力发展液冷技术。
从技术层面来看,冷媒直冷技术操作起来难度系数大,同时还存在一定的缺点,主要体现在冷板设计与策略控制上。
(1)均温难达到
冷媒直冷技术最大的技术难点在于电池蒸发器的均温设计上,必须满足电池的均温要求,而电池系统内电芯之间的温差不超过 5℃。
对于电池包来说,不光要保证电芯工作在合理的温度下,还要将不同模组之间的温差不超过一定值,这项难题也是直冷冷板需要解决的问题。
(2)耐压与密封问题
制冷剂系统蒸发压力可以达到 3-4 个大气压(一个菲仕乐的高压锅最大耐压 150kPa——1.5 个大气压),液冷冷板工作压力大概最多在 1.3 个大气压以内,考虑冷媒直冷技术的泄漏率与气压的平方与粘性系数成正比,而根据阿伏伽德罗定律可知与物理的摩尔质量成反比,所以制冷剂冷板泄露要求是水冷板的几百倍提升。
(3)成本高,供应少
为了实现蒸发器的精确控制,最好采用的是电子膨胀阀,但若选取的是精确带控制的膨胀阀就比较贵,且可以提供设备的供应商太少了。
(4)热泵模式受限
如果是直热的话,通常压缩机出口排气压力将高达 60℃以上,冷凝温度也高于四五十度,已超出电池适温区,加上目前 R134a 制冷剂系统的极限是环温零下十多度,当温度低于极限值后热泵就无法正常工作,也无法再为电池进行加热了,配上额外的电热后这样的系统在成本上并不占优势。
(5)系统回油问题
电池直冷技术电池冷板并联在制冷剂系统中,面积越大流程就越长,因此就会引起压缩机润滑油回油的问题,在特定情况下制冷剂油将积在冷板内会造成压缩机缺油失效的情况。
(6)新问题的出现
当选择了额外的直接式加热装置用于低温加热时,就要考虑是否存在出现新的问题,为了保证其安全性就会增加一些安全设计,那么所增加的一些安全配置是否会阻挡直接式加热的优势这些都还并未用实验去证明。
当然了,上面的问题一部分是可以得到解决的,比如之前一直困扰了很多零部件供应商的一个难题 「汽液混合态的制冷剂,入口不是最低温,出口一定是过热的最高温。」 大部分的冷板类零件,很多设计师对气液两相流动与换热的知识点不熟,依旧采用的是传统供应商设计的模式,就做不出来合格的蒸发器。而这个问题的解决方式就可以参照奔驰与宝马的设计。


最后:
冷媒直冷技术对比液冷的热控制架构,会发现直冷系统在成本上更便宜,直冷系统可以去掉电池侧水泵、电池侧副水壶、电池 chiller 还有一些水管,大致算下来,单车约可节约 500 多元;同时,整车的质重也变得更轻了,约可以降低 7kg 重量。
虽然冷媒直冷技术的优势比较广,且国内的比亚迪热管理也验证了冷媒直冷技术是可行的,其 EV 车型采用的是直冷直热技术、DMI 前期车型加热采用的是加热膜技术(是因为电芯自发热加热技术的不成熟,加热膜成为了应急方案,目前 DMI 车型已经取消了加热膜),但由于直冷板设计两相循环,无论是理论上还是控制难度上克服起来有一定的困难。如此看来,冷媒直冷受到了技术的限制,应用率不高,推广也就无法实施,这也是为何当前市场主流依旧采用的是液冷方案,而不推广冷媒直冷技术。
不过,我们相信冷媒直冷技术未来可期,毕竟在电动汽车对电池能量密度、快充速度要求越来越高时,在保持安全的情况下,直冷技术做到降低成本,减少部件的同时,还有着体积小、重量轻、制冷速度、性能等优势,后续待技术进步后是可能应用在更多的车型中,为整车带来更高的续航里程。