作者 I 小董同学
编辑 I Chris
▎上周去通用旗下的武汉奥特能工厂瞧了一瞧。
武汉奥特能工厂是除上海金桥奥特能工厂外的第二家工厂,目前负责别克 Eletra E5 的生产工作,未来别克基于奥特能平台打造的其他电动车也会在这里进行生产,例如下一款基于奥特能平台打造的别克 E4。鉴于奥特能平台刚刚推出 2 年多的时间,想必在未来 5 年左右的时间,别克的纯电动车都将出自该工厂。

别克 Electra E5 虽未正式上市,但试装车已经下线。除了工信部公布的信息外,E5 电池包将采用专属的 811 配方电芯,前驱版本 CLTC 续航里程可达 600 km。
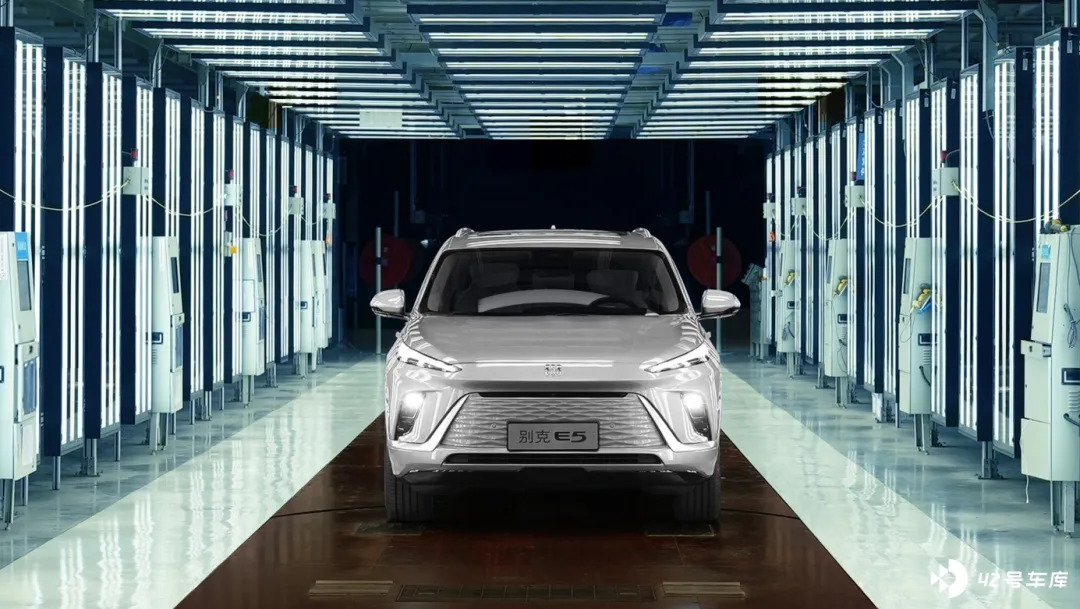
E5 电池包内部与大哥凯迪拉克 Lyriq 采用了相同配方,不过 Lyriq 采用了 12 模组组合,E5 则分为 10 模组和 8 模组两种组合。因此我们也可以通过 Lyriq 的 95.7 度电池容量猜测一下,E5 将分为 80 度电和 64 度电两个版本。
前驱版 E5 将采用 180 kW 永磁电机,四驱版将会采用前永磁 + 后异步电机的产品组合,后桥将会采用一台小功率的异步电机。
接下来进入正题,这次别克将电池和电驱进行了拆解展示,同时制造过程也完全公开。借着别克这次活动,一起来看看电池和电驱里面长什么样?
电池安全有何不同?
▎电池安全一直是新能源车的重中之重,也是痛点所在。
解决电池安全这个问题就要从两方面来解决了,一方面是预防起火,另一方面则是起火后的应对措施。
奥特能这块电池包采用来自宁德的 NCM 811 电芯,相比 523 电芯来说,虽然能量密度更高,但稳定性略弱。所以电池的温度控制成为第一环要解决的问题。这块电池在设计之初就对电芯的正极配方进行改进,掺杂稀土元素,减少氧移动,从而提升电芯的热稳定性。

每个电芯均配备了排气通道(上图中电芯上方的蓝色区域),可以看到下图中电芯通过金色云母板进行一层覆盖,云母板的作用在于绝缘和隔热,防止热失控时因拉弧导致多模组电芯同时失控,同时云母板的电芯排气通道处还进行了开窗设计,便于热失控时热量排出。
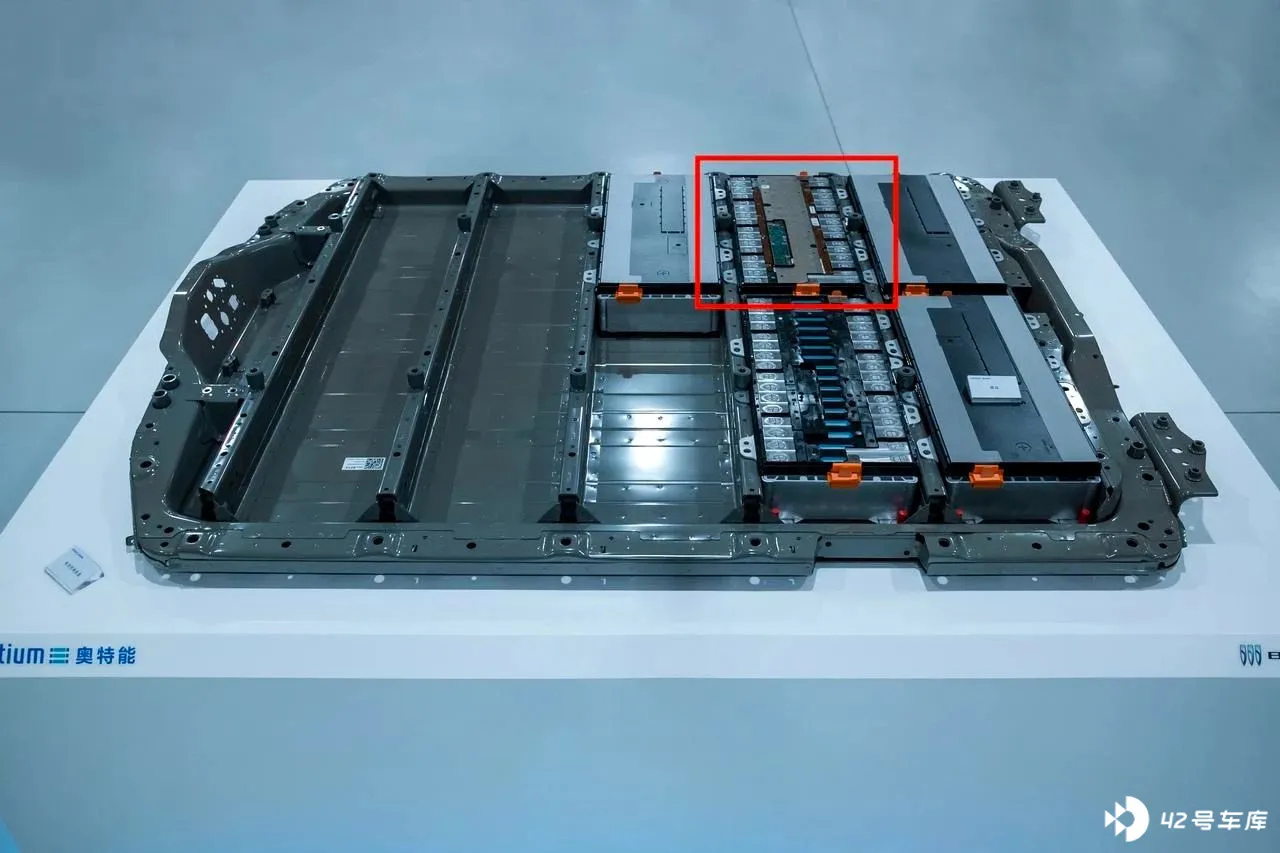
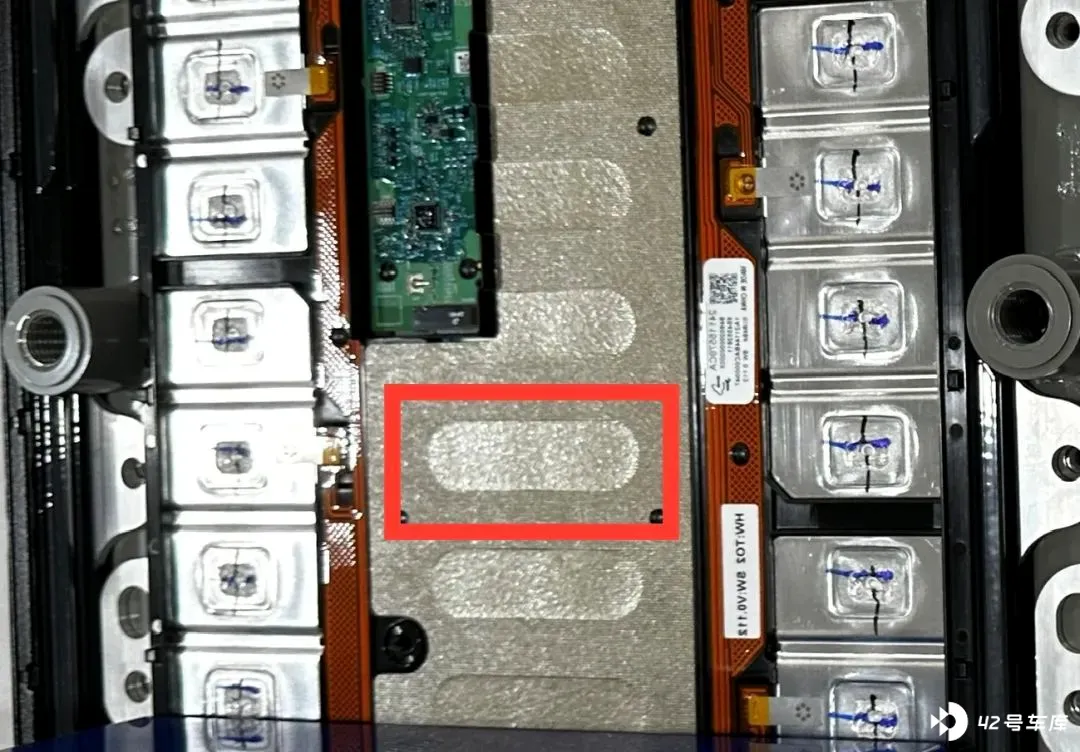
除了防拉弧设计,电芯之间还铺设了气凝胶,减少热量传递。而在每个模组下方都铺设了单独的液冷板,保证每个模组的散热能力能够维持一致。

通过改进正极配方、铺设气凝胶、独立液冷板三点能够有效降低热失控发生的几率。那么如果发生热失控,这块电池包该怎么应对?
上文提到过的防拉弧设计能够有效降低多模组电芯同时失控,单模组热失控后,热量聚集后防爆阀会自动弹开,快速排出高温气体,避免「伤及无辜」。

与此同时,在电池包上盖板部分采用由高硅氧布、气凝胶(在内部)和玻纤布叠放构成的防火毯,来确保电池包的热量不会传导至座舱,将热量从底部防爆阀排出,保障乘员舱的安全。

说完内部,再来聊聊电池壳体,除通过多根 1500 MPA 的高强度钢横梁形成井字形来提升整体的强度外,上盖总成也采用了 1500 MPA 的侧边防护梁,托盘总成也采用了 1000 Mpa 的底部防护,来降低车辆发生碰撞时,电池受损的情况。

以上都是对电池的「硬」保护,再来看看「软」保护。
车 & 云结合对 E5 的电池包进行 24 小时的电池健康监测,每秒 10 次检测频率,如发现电芯有热失控风险,模组或周边模组的 CMU(无线通讯单元)将会主动唤醒电池管理模块进行急速冷却,从而尽早发现电芯异常,防患于未然。
车云结合监控近两年已经有越来越多的车型配备,不过还没有车企公布过具体的数据,效果到底如何呢?在这里画个问号。
多层防护让奥特能平台下的这块电池包取得非常好的实验室数据,例如挤压试验 3 倍于国标要求、2 米高度跌落试验和电池包针刺后无明火、不爆炸、无热失控等等多种超过国标的安全试验。在实际参观工厂的过程中我也能感觉到,奥特能对自家电池包封装的标准、检测和执行上都保持着严苛的要求。
高强度壳体、模组、定制的电芯、多重电池热管理技术让奥特能这块电池包取得出色的安全成绩。不过,天平的另一端是这块电池包的能量密度。
即使是 811 电芯,采用电芯 - 模组 - 电池包的结构模式让奥特能这块电池包的整包能量密度并不高,只能达到 160 Wh/kg。基本是目前 CTP 结构下 523 电芯成包的能量密度,2 月 10 日亮相的智己 LS7 更是采用 6 系单晶高镍的电芯将整包能量密度提升到了 195 Wh/kg。
低能量密度带来整车重量的提升,有 wBMS(无线电池管理系统) 加持的凯迪拉克 Lyriq 单电池包重量依旧达到了 600 kg,师出同门的悍马 EV 仅电池包(212 度电)的重量更是达到了 1.3 吨。
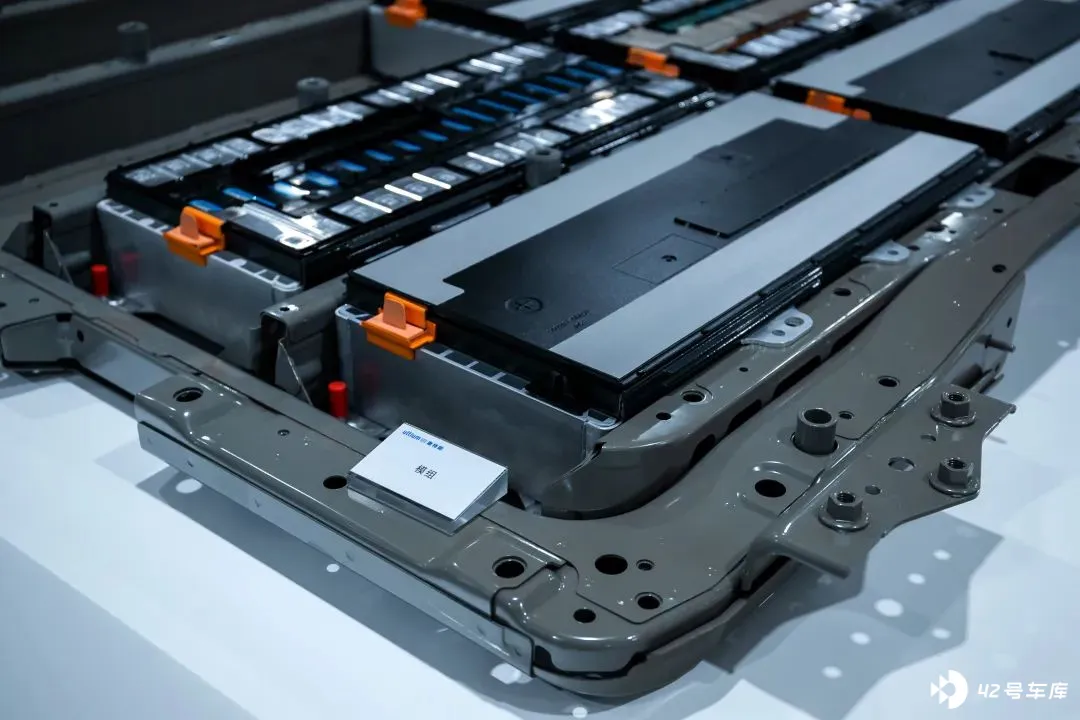
与此同时,奥特能这块电池包的高度达到 150 mm,对于奥特能平台旗下的轿车来说,驾乘坐姿怕是一个较为棘手的问题。
至于好坏,每个车企都对电池包有着不同的解读,基于他们的历史、品牌调性和用户需求等多方面的考虑因素,最终做出平衡。
拆开电机看一看
▎在电池工厂的另一侧则是动力总成的生产基地。
君威和君越的 1.5T 发动机就来自这里,不过今天的主角依然是别克 E5 前桥上那颗 180 kW 的永磁电机,这也是我第一次近距离观看电驱组装过程和拆分之后的样子,那么电驱是如何组成和工作的呢?
首先是电机定子,近两年常常能够听到扁线电机,其中的定子组件就是由通过定子铁芯 + Hari-pin (发卡)绕组组成。定子组件是决定电机性能的关键,也就是说你的车省不省电,能跑多快都跟 Ta 有关系。
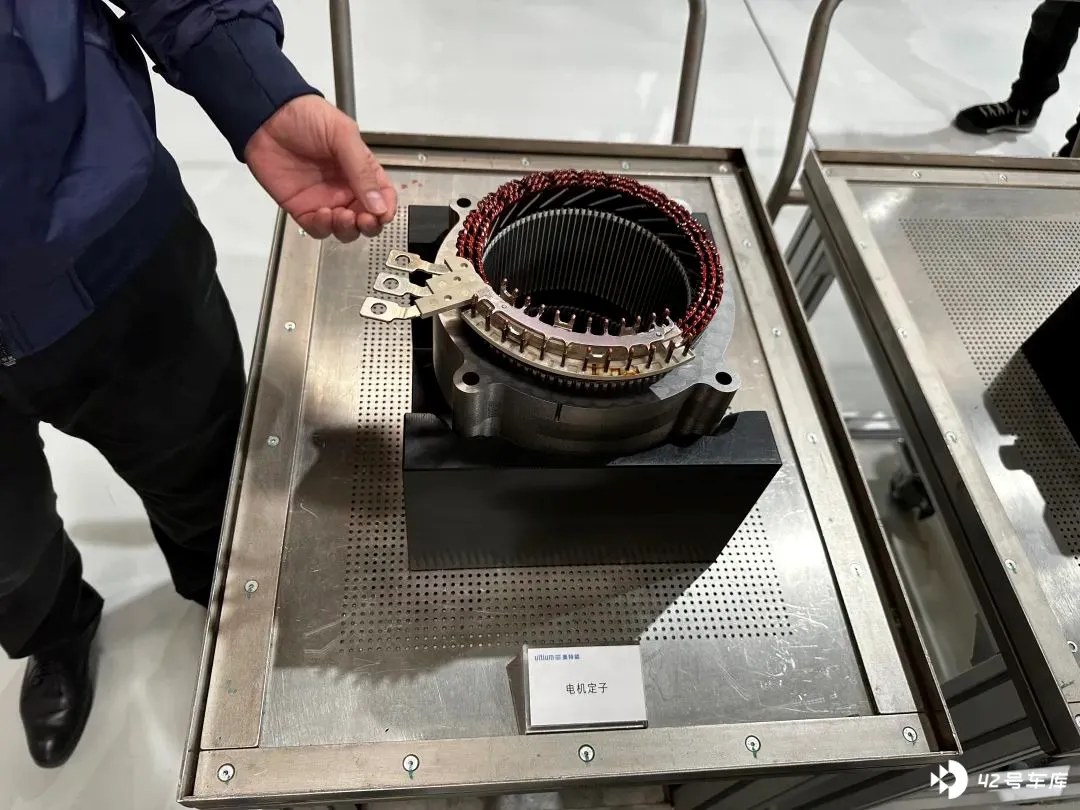
相比曾经的圆线电机,扁线电机有着更高的效率、功率密度、散热能力以及 NVH 表现。其实理解起来很简单,图中红色部分的绕组方式明显高于圆形电机的槽满率。
扁线电机其实在 2015 年就应用到了丰田第四代普锐斯上,只不过国内从 2020 年开始才开始普及,岚图、蔚来、极氪等等均采用了扁线电机,现阶段 8 层发卡绕组电机已经逐渐成为主流,所以大部队的永磁电机效率已经高达 96% - 97%,在仰望 U8 上的永磁电机效率已经达到了 97.7 %。
当然,定子铁芯也承担了一部分提升 NVH、热传导效率的责任。
其次是电机转子,顾名思义电机的转子就是在工作时能够快速旋转的零件,下图就是一个永磁体的转子。定子和转子带动齿轮,就完成了电机的工作形态。

以上只是电机运转的简单逻辑,不可能直接把转子和定子放到车上,这时候就需要一个壳体来承载他们。从图中壳体的上方可以看到一些小孔,这些小孔的作用就是给定子进行冷却。之前较为常见的冷却方式是水冷,水冷的散热效率是较低的。所以可以在一些评测的节目中看到,一些纯电车型在急加速几次之后,就会限制动力输出来进行散热,保障永磁体不消磁。

近两年主打性能的纯电车型均改为油冷进行冷却,从而提升散热效率,也保证了连续加速的抗衰减能力。
以上就是简单的解释了我们常常听到的油冷扁线电机优势所在。
再回到电机是如何驱动车轮这个问题上,这要提到一个「关键先生」—— 减速箱。驱动电机的转数基本都在 16000 - 20000 转的区间,这个转数直接应用到车轮上是不可能的,显然与整车的速度区间无法进行匹配,扭矩也是不够用的。
所以减速箱就成为了一个重要零件,通过齿轮放大扭矩和降低转数匹配车速,原理就是小齿轮带动大齿轮形成不同齿比,这里就不再展开了。

这款奥特能旗下的 180 kW 的电驱系统除了将电机定子、转子、减速箱这些集成在一起之外,还有电机控制器、交流充电模块、12 V 高低压模块等 7 or 8 合 1 的驱动单元设计。
此外,奥特能的电驱还有一点小心思就是减速箱箱体内的一个驻车设计,通过机械锁止结构,确保车辆驻车时不会溜坡,提升安全性。

整个电驱的安装流程绝大部分都由机械臂来完成,毕竟电机的装配精度要控制在 50 μm 以内,和一根头发丝的直径差不多。除了大规模自动化装配外,还要对电驱进行密封、绝缘、功能等多项性能测试。这台 3D 视觉机器人进行质检的过程让我印象深刻~

这次去武汉的奥特能工厂还是收获颇多的,工程师现场讲解让我「知其然,知其所以然」的感受极好,从电池包和电驱的拆分结构,再到它们是如何由零件组成整体,理解一些在工程设计中的巧思,这或许就是汽车工业的魅力吧~